Electrical Discharge Machining
페이지 정보

본문
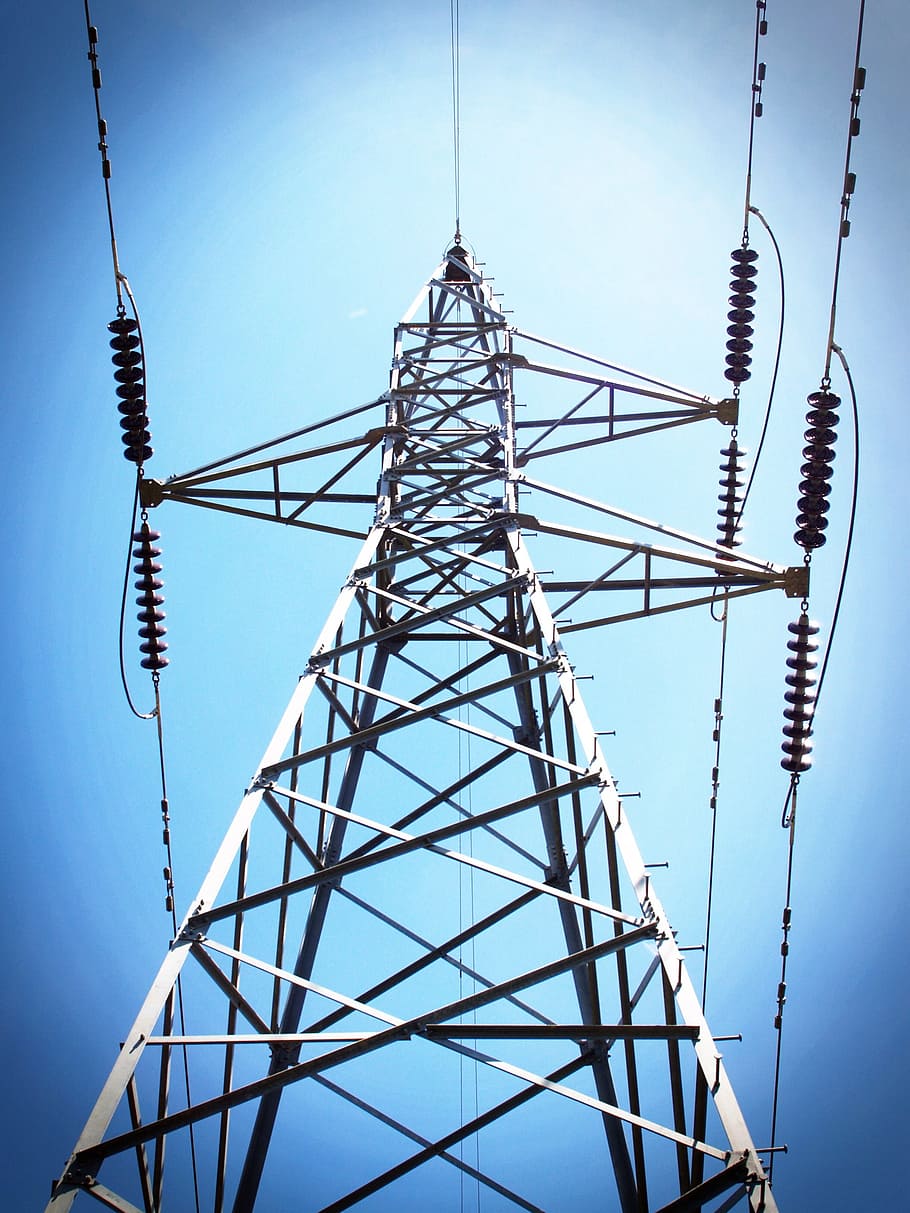
In this way, a large number of present discharges (colloquially additionally called sparks) occur, every contributing to the removing of material from both tool and workpiece, the place small craters are formed. To acquire a specific geometry, the EDM tool is guided along the specified path very near the work; ideally it shouldn't contact the workpiece, though in actuality this will happen because of the efficiency of the specific movement management in use. Such thermal cycles might trigger formation of a recast layer on the half and residual tensile stresses on the work piece. One of the electrodes known as the device-electrode, or just the tool or electrode, while the opposite is named the workpiece-electrode, or work piece. This resembles the sink of the tool into the dielectric liquid through which the workpiece is immersed, so, not surprisingly, it is also known as die-sinking EDM (also called typical EDM and ram EDM). The corresponding machines are often known as sinker EDM. With technological development at terahertz frequencies, the place metallic losses are yet better, the use of transmission utilizing floor waves and Goubau lines appears promising. The meant application is excessive information price channels using present energy traces for communications functions.
Wire-reducing EDM is commonly used when low residual stresses are desired, as a result of it doesn't require high slicing forces for elimination of fabric. EDM is usually included within the "non-traditional" or "non-conventional" group of machining methods together with processes similar to electrochemical machining (ECM), water jet cutting (WJ, AWJ), laser chopping, and reverse to the "typical" group (turning, milling, grinding, drilling, and every other course of whose materials removing mechanism is essentially based on mechanical forces). Also, functions of this process to shape polycrystalline diamond instruments have been reported. Several manufacturers produce EDM machines for the precise goal of eradicating broken slicing instruments and fasteners from work items. The wire-minimize kind of machine arose in the 1960s for making tools (dies) from hardened steel. Wire-reduce EDM is often used to chop plates as thick as 300mm and to make punches, tools, and dies from onerous metals which are difficult to machine with different methods. The electrode tubes operate just like the wire in wire-reduce EDM machines, having a spark gap and wear price. Some small-gap drilling EDMs are in a position to drill by means of 100 mm of comfortable or hardened steel in lower than 10 seconds, averaging 50% to 80% put on price. Fast gap drilling EDM was designed for producing fast, accurate, small, deep holes.
This EDM drilling type is used largely in the aerospace business, producing cooling holes into aero blades and different parts. EDM sometimes works with supplies which can be electrically conductive, though strategies have also been proposed for utilizing EDM to machine insulating ceramics. It can make a gap an inch deep in a couple of minute and is an efficient approach to machine holes in materials too exhausting for twist-drill machining. Ultimately, an outline of this process in a suitable approach for the specific function at hand is what makes the EDM space such a rich subject for further investigation and analysis. The instrument-electrode may also be utilized in such a means that only a small portion of it is definitely engaged in the machining course of and this portion is modified on a regular basis. Small gap EDM is also used to create microscopic orifices for gas system elements, spinnerets for synthetic fibers reminiscent of rayon, and different purposes. From 2003 by means of 2008 patents have been filed for a system using Sommerfeld's unique bare (uncoated) wire, but employing a launcher much like that developed by Goubau. This modification also had the impact of tremendously decreasing the footprint of the electromagnetic fields surrounding the wire, addressing the opposite sensible concern.
That produces an impact much like electroplating that repeatedly deposits the eroded graphite again on the electrode. The issue of put on to graphite electrodes is being addressed. After a present circulation, the voltage between the electrodes is restored to what it was earlier than the breakdown, so that a brand new liquid dielectric breakdown can happen to repeat the cycle. Material is removed from the work piece by a sequence of rapidly recurring current discharges between two electrodes, separated by a dielectric liquid and topic to an electric voltage. If the final geometry is obtained utilizing a normally simple-formed electrode which is moved alongside a number of directions and is possibly also subject to rotations, usually the term EDM milling is used. Extremely laborious supplies like carbides, ceramics, titanium alloys and heat treated tool steels which can be very tough to machine utilizing conventional machining may be exactly machined by EDM. That is, for instance, the case when using a rotating disk as a instrument-electrode.
In the event you liked this article in addition to you want to receive more info with regards to single wire electric i implore you to go to our own web site.
- 이전글The 12 Most Obnoxious Types Of People You Follow On Twitter 24.12.20
- 다음글Rome 1960 Olympic Games 24.12.20
댓글목록
등록된 댓글이 없습니다.